TECHNICAL PAPER #63
UNDERSTANDING HYDROPONICS
By
Mark Anderson
Larry Bloom
Charles Queen
Mona Ruttenberg
Kristine Stroad
Samart Sukanit
Dan Thomas
Technical Reviewers
Ralph P. Prince
Walter G. Rosen
Ronald A. Stanley
Published By
VITA
1600 Wilson Boulevard, Suite 500
Arlington, Virginia 22209 USA
Tel:
703/276-1800 . Fax: 703/243-1865
Internet: pr-info@vita.org
Understanding Hydroponics
ISBN: 0-86619-282-4
[C]1989, Volunteers in Technical Assistance
PREFACE
This paper is one of a series published by volunteers in
Technical
Assistance to provide an introduction to specific
state-of-the-art
technologies of interest to people in developing countries.
The papers are intended to be used as guidelines to help
people choose technologies that are suitable to their
situations.
They are not intended to provide construction or
implementation
details. People are
urged to contact VITA or a similar organization
for further information and technical assistance if they
find that a particular technology seems to meet their needs.
The papers in the series were written, reviewed, and
illustrated
almost entirely by VITA Volunteer technical experts on a
purely
voluntary basis.
Some 500 volunteers were involved in the production
of the first 100 titles issued, contributing approximately
5,000 hours of their time.
VITA staff included Suzanne Brooks and
Patrice Matthews handling typesetting and layout, and
Margaret
Crouch as editor and project manager.
Co-authors Mark Anderson, Larry Bloom, Charles Queen, Mona
Ruttenberg, Samart Sukanit, and Dan Thomas originally wrote
up
this project as a thesis for their curriculum in technology
education at West Virginia University in Morgantown, West
Virginia,
under the guidance of Dr. Edward Pytlik.
Kristine Stroad
is a freelance technical writer/edit who has experience in
Kenya,
in Thailand for VITA, and with the United Nations in Geneva.
VITA Volunteer reviewer Ralph Prince is an agricultural
engineer
with the John F. Kennedy Space Center in Florida.
Reviewers
Walter Rosen and Ronald Stanley are also VITA
Volunteers. Dr.
Rosen, a botanist, is on the Board of Biology for the
National
Research Council.
Dr. Stanley, senior biological policy analyst
at the U.S. Environmental Protection Agency, is a plant
physiologist
with experience in Greece, Hong Kong, China, and the
Caribbean.
VITA is a private, nonprofit organization that supports
people
working on technical problems in developing countries.
VITA
offers information and assistance aimed at helping
individuals
and groups to select and implement technologies appropriate
to
their situations.
VITA maintains an international Inquiry Service,
a specialized documentation center, and a computerized
roster of volunteer technical consultants; manages long-term
field projects; and publishes a variety of technical manuals
and
papers.
UNDERSTANDING HYDROPONICS
by Mark
Anderson, Larry Bloom, Charles Queen,
Mona Ruttenberg, Kristine Stroad, Samart Sukanit, and Dan
Thomas
I. INTRODUCTION
Hydroponics is the growing of plants without soil.
The name "hydroponics"
implies that the plants are grown in water.
Actually
the plants are usually grown in "growing beds"
that may be filled
with gravel or sand or other material, and they get the
nutrients
they need from a water solution added to the beds.
Some of the important advantages of successful hydroponics
over
soil culture are:
o Yields in
hydroponics can be as much as ten times greater than
in soil culture;
o Plants need less
space in hydroponics because the nutrients
are concentrated;
o The nutrient
solution is re-used, so the amount of water needed
is much smaller;
o The nutrients are
easier to test and adjust to growing conditions;
and
o Labor costs are
lower.
Another feature of a well-designed hydroponics system is
that it
does not pollute the environment.
Hydroponics is used mainly as a controlled system for the
production
of out of season crops, for growing crops in areas where the
soil is not suitable for cultivation, or where water supply
is
limited. It is also
useful for studies in plant nutrition, plant
diseases, and plant breeding, where growth under exact
conditions
is needed. Almost
any type of plant can be grown hydroponically.
Home gardeners can set up small hydroponics systems in their
homes to grow a few crops for home use.
In cold climates, large
greenhouses are used for profitable hydroponics enterprises
providing high quality, out of season produce.
A hydroponics
enterprise in a warm climate could also be feasible, using a
locally-built screened structure to give a growing
environment
that can be kept free from insects and other pests and
reduce
heat and humidity.
Hydroponics is intensive agriculture that makes sense in a
world
where farmlands are disappearing and there is a need for
quality,
locally-produced food.
This paper will describe the basic features of a medium- to
large-scale hydroponics system and prefabricated greenhouse
appropriate
for cold climates.
Some modifications for a system
suitable for hot climates are also discussed.
Home gardeners in
any climate can use the basic theories contained here, but
may
want a simpler operation, possibly without a greenhouse or
special
structure.
II. SYSTEM DESIGN
Site Selection
In choosing a good site for a medium- or large-scale
hydroponics
system, the following should be considered:
o The site should be
reasonably level;
o The site should be
as free of trees and shrubs as possible;
o There should be a
supply of suitable gravel, sand, lava, or
other mineral
material available nearby;
o For a commercial
enterprise, the site should be within reasonable
reach of the
markets where the produce will be sold;
o Roads and
communications to the site must be good, to allow
for the delivery
of materials and other equipment, and for the
shipment of
produce;
o Depending on the
climatic conditions, the site should have a
good southern
exposure to make use of solar energy; and
o Water,
electricity, gas, etc., as needed for present or future
use, should be
available at the site.
Greenhouse Design and Construction
A greenhouse is necessary in cold climates to provide a
controlled
environment for the successful growing of high quality
plants
throughout the year.
In warm climates, a greenhouse is unnecessary,
and a simple structure with a wood, tile, slat, bamboo, or
thatch roof to provide partial shading and a dirt floor with
pits
containing suitable mineral material is recommended.
A more advanced
structure could include a concrete block foundation,
concrete
floor, and screened walls.
Adobe might be considered for
the foundation.
In cold climates, a greenhouse makes possible year-round
cultivation.
In a climate with hot days and cool nights, the greenhouse
provides a controlled environment that not only protects
plants
from cold at night, but reduces heat and humidity during the
day.
If light is likely to be limiting at any time of the year,
greenhouses
should be positioned to get the most sunlight.
This means
the long side of the greenhouse should lie east to west as
shown
in Figure 1.
uhn1x3.gif (486x486)
In designing the interior of a greenhouse, first consider
the
amount of growing space needed and the size of the land
available.
Then think about the operations involved, automation, energy
considerations and costs, and future expansion.
Include areas
for preparing the nutrient solution and for storage.
In a commercial greenhouse, an office and service area is
needed
for administration and to prepare, grade and pack crops for
sending
to market. An office
should have space for visitors and customers,
a secretary, and a manager.
An employee lunch room, a
lavatory, and a parking area are also needed.
The office and
service area should have sound absorbing material in the
wall
next to the growing area to protect the area from the sounds
made
by the greenhouse fans.
There are several advantages to constructing a series of
connected
greenhouses, with adjoining walls and connected roof
gutters:
o They require less
land area than detached greenhouses;
o Fewer construction
materials are needed for side walls; and
o Less energy is
required to heat or cool because there are fewer
exposed wall
surfaces.
In cold climates, a disadvantage is the difficulty of
removing
snow from the gutters between connected greenhouses.
(Heat lines
can be placed under the gutters to melt the snow.)
Office and
service areas can be located in an adjoining building on the
north side of the greenhouses, decreasing heat loss.
Prefabricated buildings may be considered, where
available. Materials
and labor costs will vary locally and should be compared.
Replacement parts for prefabricated units can be ordered
from the
manufacturer.
Fiberglass (with Mylar), polyethylene film, and glass can be
used
for greenhouse roofs.
Fiberglass panels are made of reinforced
plastic and are flexible enough to fit into curved
frames. Mylar
is a type of polyethylene, and is used as the inner layer
with
fiberglass.
Fiberglass with Mylar lasts much longer and transmits
light better than a double layer of polyethylene.
The highest
quality of polyethelyne film--six millimeter (0.23
inch)--lasts a
maximum of a year and a half.
Fiberglass with Mylar can last 15-20
years. Glass can
also be used, and lasts much longer than even
fiberglass, but it is much more expensive than either
fiberglass
or polyethylene.
Whatever the material, it is recommended that
double layers are used; the air between the layers acts as
insulation
and reduces heat loss.
To reduce start up costs, a new hydroponics enterprise may
want
to consider starting out with polyethylene and changing to
fiberglass
after one to two years.
Acrylic sheets can be used for the greenhouse side walls and
some
parts of the end walls.
Acrylic sheets are stiff, are highly
resistant to impact, insulate heat, and transmit light
well--about
73 percent.
Compressed limestone gravel, six inches (15 cm) thick for
good
drainage, is recommended for the greenhouse floor.
Other types of
gravel, or sand or dirt could also be used.
Pathways in the greenhouse, made of asphalt, or concrete,
should
be wide enough for a cart to pass through easily--about six
feet
(1.8 m) wide--if carts are ever expected to be used in the
operation.
The greenhouse foundation does not need to be continuous
around
the base of the building.
Poured concrete footings can be placed
one foot (30 cm) below the frost line in cold climates.
Gas-fired unit heaters, are used when necessary to blow warm
air
to fan jets (see Figure 2), which hang between them.
The fans
uhn2x5.gif (540x540)
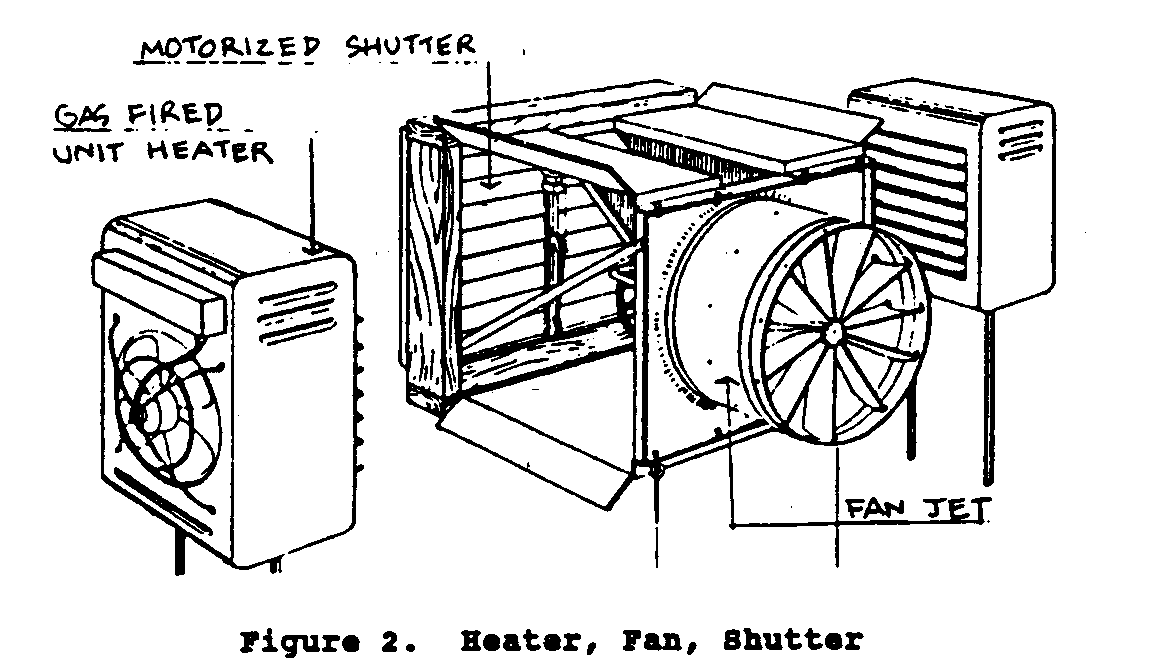
distribute the warm air through a polyethylene tube to the
entire
growing area (see Figure 3).
Heat escapes in small jet streams
uhn3x6.gif (600x600)
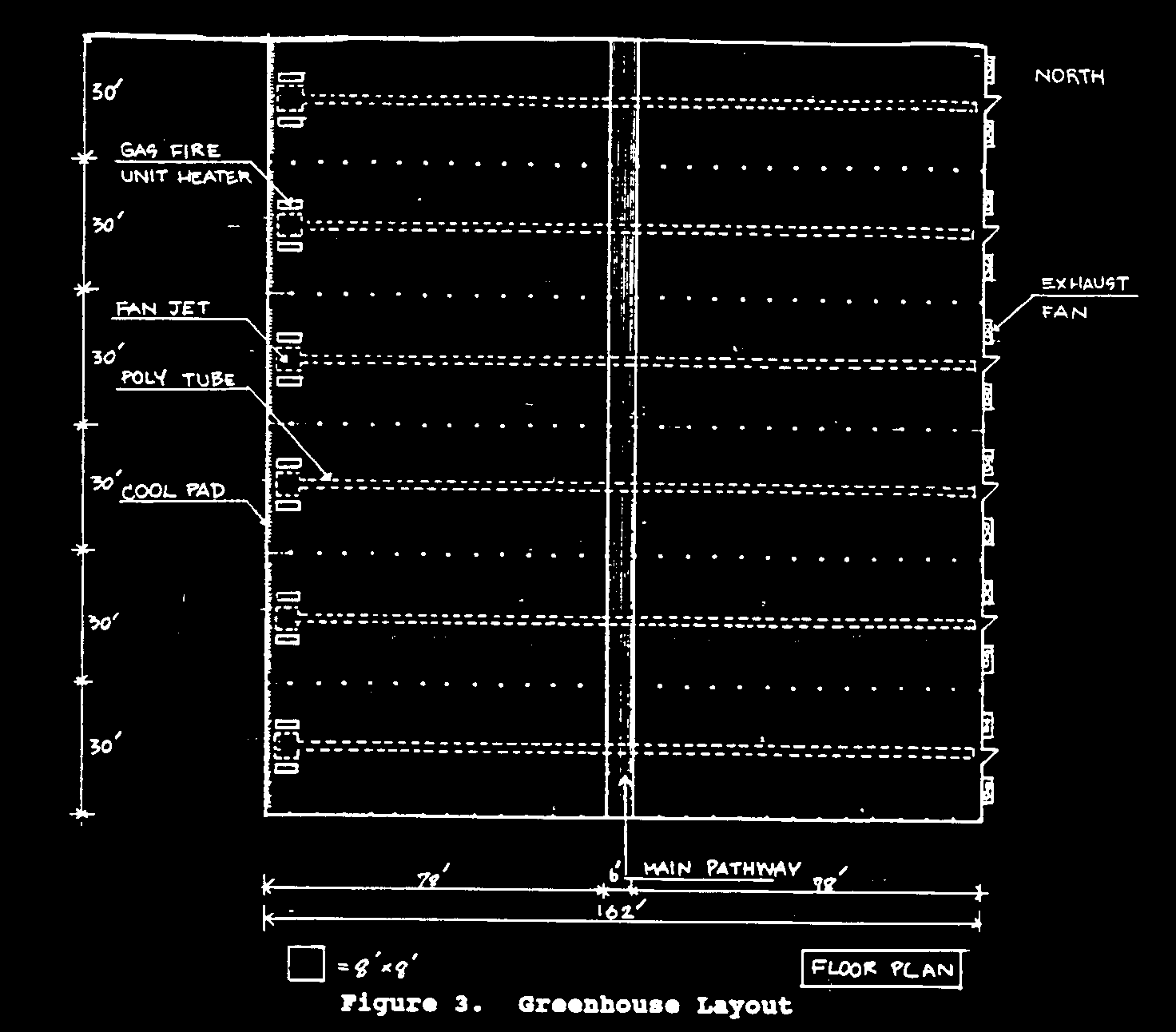
from holes on either side of the tube.
The heat mixes rapidly
with the surrounding air and sets up a circulation
pattern. Thermostats
should be located at the height of the plants, to measure
the greenhouse average temperature.
An insulating ceiling cover is stored on a reel and rolled
out at
night. In the
morning, a wheel attached to the reel is turned to
roll the cover back to the storage position.
A cover with an
insulating value of R-4 insulates much less than normal
ceiling
insulation, but saves a lot in heating costs.
The cost of such a
ceiling cover can be regained in three years in savings on
heat.
Ventilation is needed, to:
o Reduce air
temperature when it becomes too hot;
o Exchange air to
renew the supply of carbon dioxide for photosynthesis;
and
o Reduce the
relative humidity in the greenhouse.
In hot weather, large volumes of air must be cooled and
brought
into the greenhouse.
The coal air must pass in a smooth stream
through the entire growing area.
A cooling system using evaporation
is used for this purpose.
A 30-inch (76 cm) fan is hung between two unit heaters
(where
needed). The fan
blows air into the polyethylene tube, which is
attached to the fan jet.
The air blown into the tube may come
from the heaters, the outside of the greenhouse, or from the
inside of the greenhouse, depending on the temperature and
humidity
required. Continuous
circulation within the greenhouse is
set up by controlling heaters, fan jet, and shutters.
The shutters
prevent fresh outside air from passing to the fan jets when
it is not needed.
The shutters may be motorized or not, according
to labor and equipment costs.
The cooling system is based on the process of heat
absorption
during the evaporation of water.
Along the western wall of the
greenhouse, water passes through vertical pads.
There are two
exhaust fans on the opposite wall, drawing the air from
inside
the greenhouse to the outside (see Figure 3).
Warm outside air is
drawn through the pads at the same time.
Through evaporation,
water in the pads absorbs heat from the air passing
through. The
air coming in to the greenhouse can be as much as 10 to 25
degrees
Fahrenheit (5 to 15 degrees Centigrade) cooler than the
outside air. This
cooling system uses cooling pads, plumbing,
valves, strainers, and supports.
Two pumps and reversible drive
motors are used to recycle the water in the pads.
While natural sunlight should be used wherever possible,
supplemental
lighting is sometimes needed in the greenhouse.
Lighting
fixtures holding two 90-watt fluorescent bulbs are used in
our
sample greenhouse.
The bulbs are turned on an average of 12 hours
per day in their cold climate.
In tropical areas overheating due
to excessive natural sunlight will often be a more serious
problem
and shading has to be provided.
The growing beds in the sample greenhouse are constructed of
fiberglass, 25 feet (7.6 m) long, three feet (91 cm) wide,
and 10
inches (25 cm) deep.
The beds are placed in clusters of six beds
each. Support for
the beds is provided by two-by-fours (5 cm high
by 10 cm wide pieces of wood) made into a frame.
The tops of the
beds are four feet 1.2 m) off the ground so that the space
underneath
can also be used for growing.
The bottom of each bed should
be sloped for good drainage.
Beds may also be made of wood, concrete,
or metal, but should be painted with a high-grade
asphalt-base
paint on the inside.
Porcelain, pottery, or glass containers
may be used in smaller systems.
Gravel, sand, cinders, shale, coral limestone treated with
phosphate,
wood shavings, vermiculite, perlite, plastic chips, or
other material can be used as the medium in the growing
beds.
The more inert the material the less likely it is that
problems
will develop. For
example, wood shavings generally contain chemicals
that inhibit plant growth; these may leach into the nutrient
solution or be taken up by the plant roots and stunt the
crop.
Similarly, untreated limestone usually will increase the pH
of
the growing medium; acid-loving plants would not be able to
grow
in such a medium.
The size should be from 1/16 to 1/2 inch (1.58 mm to 12.7
mm)
diameter, with no sharp edges that could cut the roots of
young
plants. Gravel
should be 1/4 to 1/2 inch (6.4 to 12.7 mm)
diameter. When the
plants grow, their root structure grows down
into the medium.
Once a year the medium should be replaced, and
the growing beds sterilized.
This might be accomplished by flushing
with a large amount of near-sterile water (for example,
"clean" ground water) or by using a chemical, such
as sodium
hypochlorite. If a
chemical is used, the residues need to be
taken into account.
For example, sodium hypochlorite will leave
residues of sodium chloride (ordinary salt), which might
stunt
crops that are especially sensitive to salt.
Pipes used should be iron or plastic.
Galvanized pipe should not
be used since zinc from the galvanizing will cause trouble
with
the nutrient solution.
Nutrient Solution and Delivery
The nutrient solution is the heart of the hydroponics
system.
The plants get the basic chemicals needed for successful
growth
from the solution.
Nutrient solutions can be purchased ready-mixed in some
countries,
or they can be mixed by hand.
Hand mixed solution is recommended
over ready-mixed, since it costs much less and the grower
has greater control over the contents.
The grower can adjust
hand mixed nutrient solutions according to plant
characteristics,
temperature, light intensity, composition of the water, etc.
Thousands of different chemical combinations have been used
successfully;
however, certain chemicals are essential for plant
growth. These
include nitrogen, phosphorus, potassium, magnesium,
sulphur, and calcium.
Trace chemicals, in much lower concentrations,
are iron, boron, manganese, zinc, and copper.
An example
of a nutrient mixture and its cost, for a commercial
hydroponics
greenhouse in the United States, is in Table 1.
Costs are given
in 1987 U.S. dollar amounts.
Native sources of nutrients, such as animal manures, might
be
usable, but can cause many problems.
Most animal manures contain
high levels of nitrogen in the form of ammonia, to which
many
plants are sensitive.
Also, manures can be a source of diseases
from organisms that infected the plants on which the animals
fed.
Perhaps most important, getting the correct balance of
nutrients
may be difficult with a source in which the concentrations
are
not clearly defined.
Nonetheless, if no other sources are readily
available, or if available sources are too expensive, it would
be
worthwhile to test some native sources on a small scale with
the
intended crop.
In a relatively humid area, .12 gallons (.45 liters) of
nutrient
solution should be used for every square foot (.3 sq. m.) of
growing area, and the solution should be changed every four
weeks. In areas with
lower humidity more solution should be used
and should be changed more often because of evaporation
losses.
The mixing tank can be made of fiberglass or other
non-porous
material. Several
mixes may need to be made to complete the solution
change. It is wise
to mix up a little extra solution in case
of spills or other accidents.
You will need enough nutrient solution
to bring the water level to 1/2 to 1 inch (1.3 to 2.5 cm)
from the top of the growing beds.
The nutrients should be mixed
first in a small amount of water.
Table 1: Nutrients Needed Per
Year
Nutrient
Essential Price/
Pounds
Total
solutions
elements pound
needed
(US$)
Sodium
nitrate Nitrogen
$0.30
216.5 $
64.95
Potassium
Potassium
sulphate
Sulphur $0.20
72.2
$ 14.44
Super-
Phosphorus
phosphate
Calcium $0.08
160.4
$ 12.83
Magnesium
sulphate
Magnesium $0.16
64.2
$ 10.27
Iron
Iron
sulphate
Sulphur $0.96
16
$ 15.63
Manganese
sulphate
Manganese $0.32
5.5 $
1.76
Boric acid
Boron $0.32
5.5
$ 1.76
Zinc
sulphate
Zinc $0.26
2.5
$ 0.65
Copper
sulphate
Copper $0.88
2.5
$ 2.20
$124.22
If there is a problem with the nutrient solution, the plants
will
show deficiency or toxicity symptoms.
You may wish to consult a
reference book such as The Guide to Commercial Hydroponics
(see
Bibliography) to know the symptoms related to each chemical.
The nutrient delivery, or irrigation, system keeps the
growing
medium damp at all times, while allowing plenty of oxygen to
get
to the roots of the plants.
The growing beds are flooded one to
three times a day for half an hour.
After flooding, the liquid is
drained back into the tank, to be reused later.
Irrigation can be
done manually, automatically by using a pump and a timer, by
a
gravity-fed system, by wick, or by drip methods.
An automated system can be constructed from one 55-gallon
(208
liters) drum, one 1/4 horsepower centrifugal pump, one
electric
timer, and 1/2 inch (1. 3 cm) PVC piping for each cluster of
six
growing beds (see Figures 4 and 5).
This automatic system ensures
uhn4x100.gif (540x540)
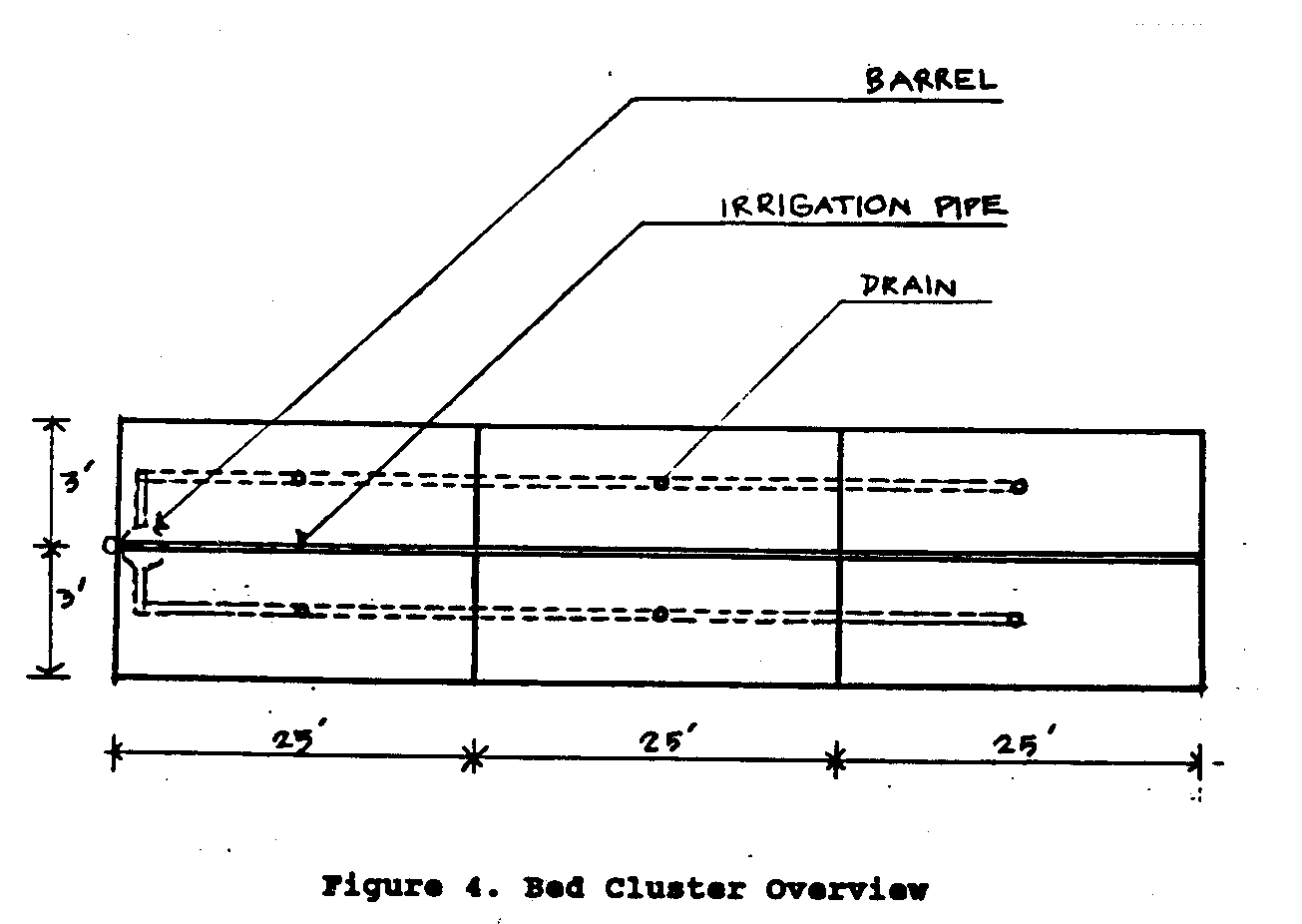
the timing and amount of nutrient solution delivered, and
reduces
labor costs.
In a gravity-fed system, the growing beds are divided into
sections,
each on a slightly higher elevation and slightly longer
than the one after it.
Two tanks of nutrient solution are used.
A larger tank is at the lower end of the beds, below
ground. It
is connected by a channel to a smaller tank at the level of
the
highest beds. The
smaller tank is filled by pump from the larger
tank before an irrigation is made.
The solution flows from the
smaller tank through all the beds, and empties into the
large
tank. The solution
needs to be pumped only once, at the beginning.
For the nutrient solution to work best, beds should be
completely
irrigated in 30 minutes or less.
The solution should be pumped at
a rate of at least two gallons per minute.
It should take one
hour for the beds to drain into the drain pipes and back
into the
solution tank. The
drain holes in the beds should be one inch
(2.5 cm) in diameter for fast drainage.
In cold weather, one irrigation every other day, in
mid-morning,
is enough. In hot
weather, three irrigations a day are recommended.
Young plants need three irrigations a day regardless of the
weather.
If three irrigations a day are done, the first should be
between
seven and nine o'clock in the morning, the second one
between ten
and twelve o'clock, and the third between two and four
o'clock in
the afternoon. An
automated system would have a timer set according
to this schedule.
As mentioned earlier, the nutrient solution should be
changed
every four weeks. In
an automated system, the solution can be
drained from the solution tanks by removing the connector
pipe
from the pump and attaching it to tubing through which the
solution
would be pumped out to the sewer, or into the ground, away
from sources of drinking water.
After the solution is drained, water should be put in the
solution
tanks and the beds flushed with water.
The water is then
pumped out to the sewer or ground.
Fifty-five gallon (208 liters)
drums, stored in the storage area, are filled with new
nutrient
solution from the mixing tank, taken to the greenhouse area
by
carts, and siphoned into the storage tanks.
Pest Control
Because the plants are grown indoors in an inert medium,
pests
are not the problem they are in soil culture.
Plants would be
very quickly contaminated, however, if disease were
introduced
into the system.
Regular replacement of the growing medium is
recommended to guard against contamination.
In order to restrict the entrance of pests from the
outdoors,
sponge pads soaked with bleach should be placed at all
entrances
to the greenhouse or building.
This will help kill pests that are
in the dirt carried by shoes., Cigarette smoking should not
be
allowed in the greenhouse, since it could introduce tobacco
mosaic,
which is harmful to tomato plants.
Observation of the plants is an important step in
controlling
pests. Plants should
be checked every day. At the first sign
of
pests, the plants and/or the insects themselves must be
removed
or destroyed. If the
pests are localized on one or a few plants,
those plants should be uprooted and removed from the growing
area. If the pests
are fairly large and/or immobile, they can be
handpicked. If a
pressurized water system is available, especially
if it is chlorinated, a vigorous spray of water may be
sufficient
to dislodge and disrupt small insects.
If these sanitation
measures are not effective, chemicals may need to be
used. In any
case, the source of the pests must be identified.
If workers have
carried them in from other greenhouses or from field crops,
steps
will have to be taken to prevent the same thing from
happening
again. If the source
is nearby infected or infested plants, those
plants may need to be removed and/or destroyed.
Also note that
some pests cannot be destroyed by burning; in fact, viruses
may
be spread by burning.
Therefore, if any diseased plants are to be
destroyed by burning, it should be done a long distance from
the
growing area.
Two pesticides that are fairly safe for plants and humans
may be
used. Whitmire's
White Fly Control Spray has low toxicity to
humans and is used to control white flies in tomato plants,
which
are highly susceptible to the pest.
The spray should be applied
every six weeks. It
is also effective against fungus gnats,
thrips, and cucumber beetles.
Rotenone, an organic contact and
stomach poison, is largely non-toxic to warm-blooded
animals. It
is particularly effective against aphids, a major carrier of
tobacco mosaic, and against chewing insects.
Because it has little
residual effect, it must be applied every two weeks.
Even
though these pesticides are not very toxic to humans, to
prevent
dust and spray inhalation, workers should wear respirators
when
applying them. As
with all chemicals, precaution should be taken
to minimize contact with the skin.
Equipment Costs
Costs for construction materials, equipment, and supplies
will
vary widely locally.
In addition to the construction materials
already mentioned, basic office equipment and shop tools are
needed.
III. PRODUCE
Careful thought and analysis should be given to the
selection of
crops to be grown.
Consult books, current seed catalogues, and
food production and marketing specialists.
Plan your crops to make the most use of space.
Plant root crops
next to leafy crops, and short, leafy vegetables in the
partial
shade of larger plants.
In a hydroponics enterprise, crops grown should be
competitive
for their superior quality and local origin.
Although there may
be one crop in particular that can be produced with superior
quality, planting a variety of crops is recommended for the
following
reasons:
o
to avoid overloading the market;
o
to protect the business from price
fluctuations; and
o
to achieve temperature control.
Information on crops selected for production in a commercial
hydroponics greenhouse in the United States is included here
as
an example. Reasons
are given for selecting the particular crops,
as are a crop rotation chart (Figure 6), the planting and
harvesting
uhn6x15.gif (600x600)
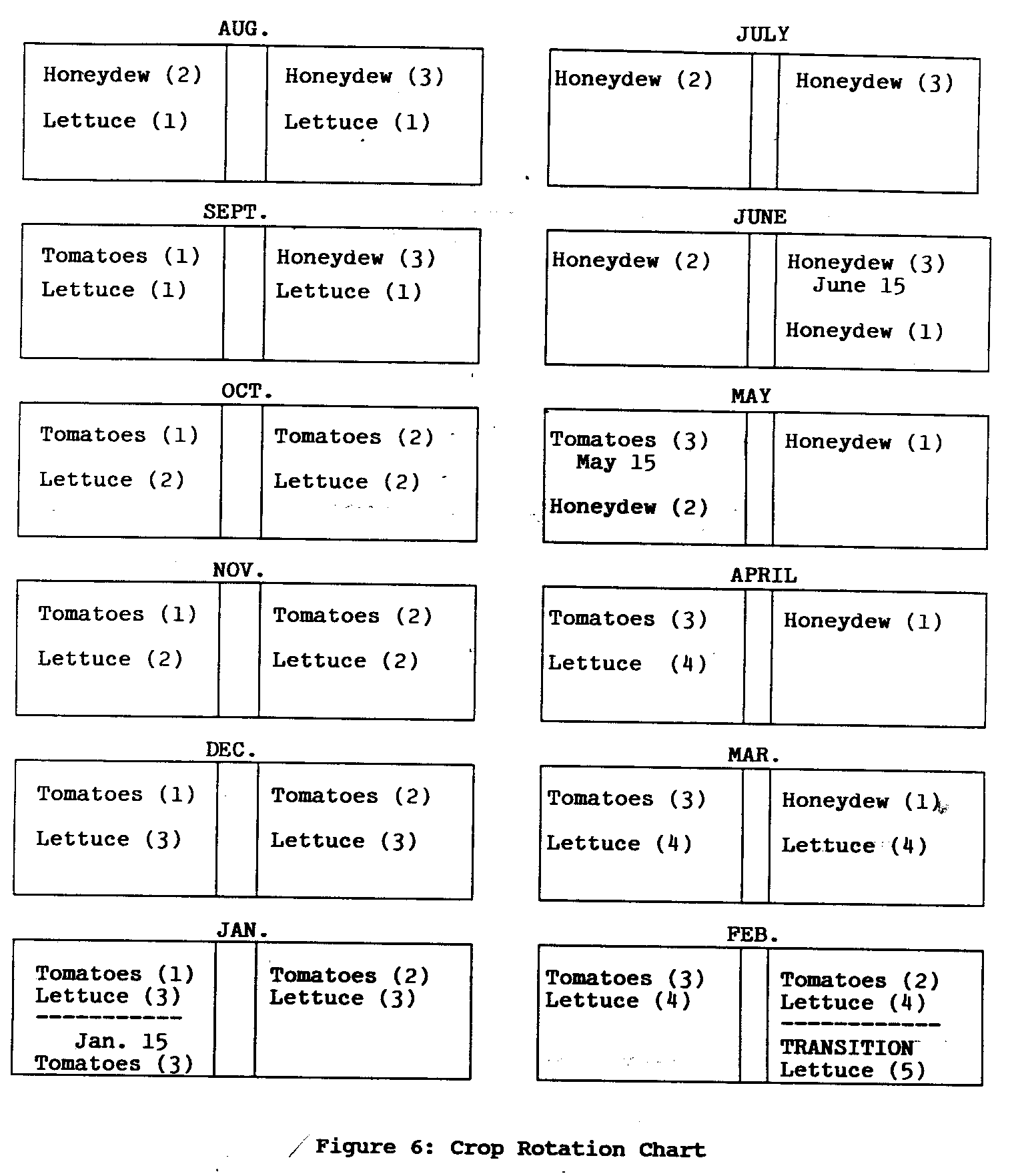
schedule (Figure 7), and the layout of the crops within
uhn7x16.gif (600x600)
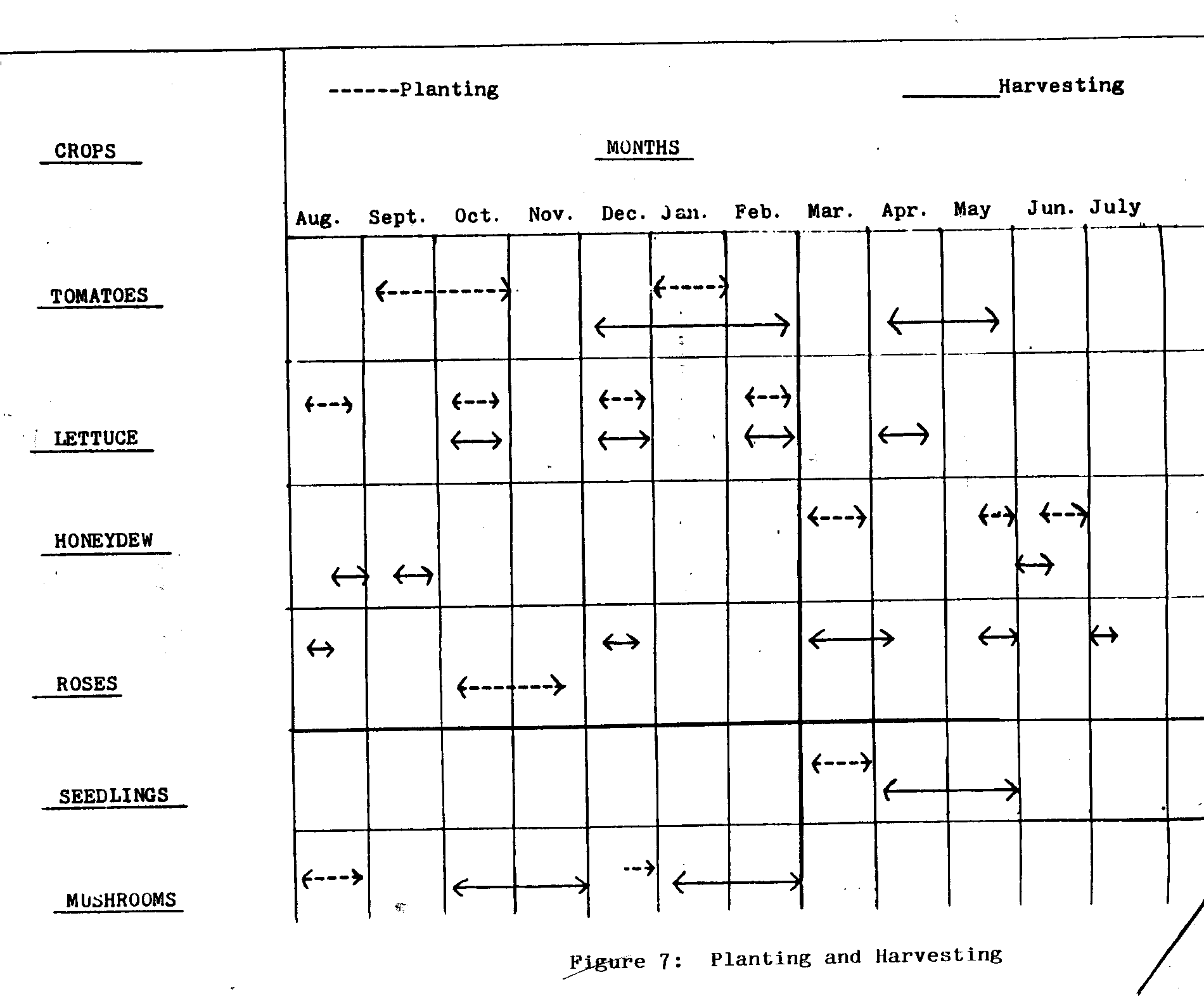
the greenhouse.
Table 2 gives crop income figures.
Table 2. Crop Production and
Yearly Income
Crop
Per plant
Per bed yr. Beds
Total
Value
(US$)
Tomatoes 16
lbs. 32 plants
270
138,240 lbs. 45,619
Lettuce 1/2
lb. 136 plants
720
48,960 lbs. 25,949
Seedlings
(1) 300 trays
18
5,400 trays 9,450
Honeydew 10
pcs. 18 plants
270
48,600 pcs. 41,310
Mushrooms 3.5
lbs/ 138 sq.ft.
432
208,656 lbs. 198,223
sq.ft.
bed
Roses 2
pcs. 75 plants
36
5,400 pcs. 4,320
The greenhouse consists of six connected sections, each one
30
feet (9.1 m) wide (for a total width of 180 feet--54.9 m) by
162
feet (49.3 m) long.
Each growing bed is three feet (91 cm) wide
and 25 feet (7.6 m) long.
The beds are laid out in pairs, with
aisles between each pair.
(See Figure 8). There are
three-foot,
uhn8x17.gif (600x600)
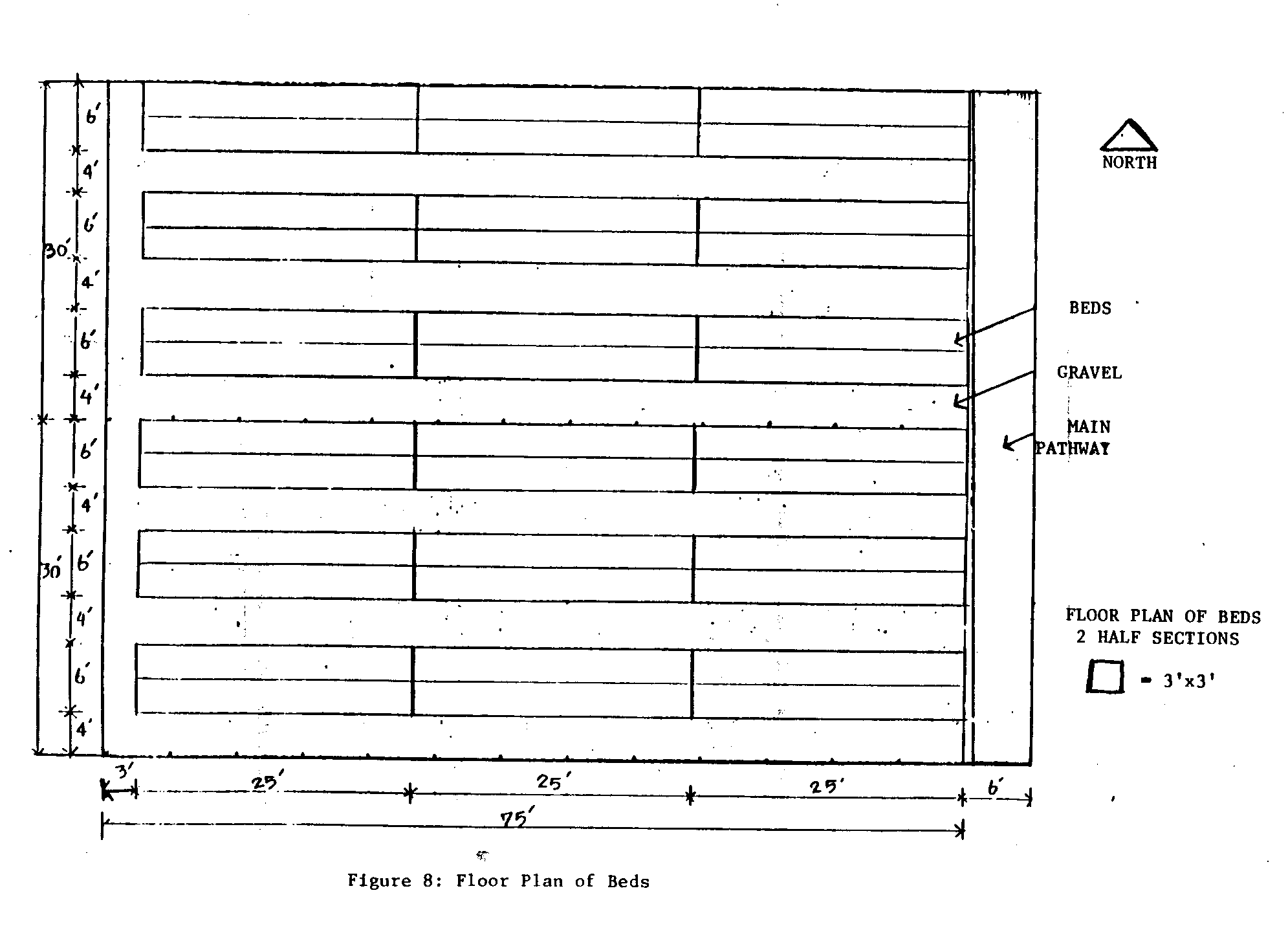
four-inch (1 m) walkways between the six foot (1.8 m) double
beds, and the greenhouse has a center aisle six feet (1.8 m)
wide.
Three crops--tomatoes, lettuce, and mushrooms--are planted
together
in one bed, between August and March.
Honeydew melons,
roses, and seedlings are also grown.
As in some other places with cold climates, off season production
of tomatoes is a good choice, since most tomatoes are
shipped
from a great distance and are picked when hard and
green. Hydroponically-grown
tomatoes are reportedly tastier and juicier than
other tomatoes. They
can be planted closer together and therefore
yield more. In this
greenhouse, tomatoes are planted in two rows,
one and a half feet (45 cm) apart.
One half of the greenhouse is
planted in tomatoes, three times a year.
That is 8,640 plants per
year. At 16 pounds
(7.3 kg) per plant, the yield is 138,240
pounds (62,800 kg) per year.
Tomato seeds are sown directly into the gravel in the
beds. The
temperature for germination and growth is 70-75 degrees
Fahrenheit
(20-25 Celsius) during the day, and 65 (17 Celsius) in the
evening. Tomatoes are
self-germinating, although some shaking of
the plants may help the process.
During the winter months fluorescent
lights are used over the beds whenever the sun is not
shining,
or at night, in order to provide the light needed for fruit
production. Each
tomato plant is staked, for maximum production
in minimum space.
Harvesting is done over a four- to six-week period.
During the
period of from 80 to 130 days after planting, harvesting is
done
every other week.
After the harvest period, the tomato plants are
uprooted and new seed sown in the same place.
In the hydroponics greenhouse, a full crop of Boston-type
lettuce,
which is popular and has high market value, can be produced
every two months.
Lettuce is planted in the same bed with tomatoes,
increasing the yield per bed tremendously.
There is no
problem with the spacing of the plants when the amount of
nutrients
is very carefully measured and fed to the beds.
The only
consideration is that the lettuce receive enough light.
Each
plant yields approximately .5 pound for a total yield of
48,960
pounds (22,228 kg) a year.
Lettuce makes a good companion to
tomatoes and honeydew melon because it needs less light and
can
therefore be grown easily between and below the other crops.
However, lettuce does not withstand heat well, and cannot be
grown during the summer months or in a hot climate.
The lettuce is harvested every 60 days.
Harvesting is easy--the
entire plant is pulled up.
Although many pieces must be picked
within a very short time (two to three days), there is
little
danger of damage or loss.
The beds are immediately replanted.
Forty-five beds of lettuce are sown per week, so that a
fresh
harvest of lettuce is ready for market every week.
The production of honeydew melons in the greenhouse is
profitable
due to the controlled conditions.
It can be planted three times a
year, instead of only one time outside.
Honeydew was chosen because
of its higher market value than either of the other more
common melon varieties--cantaloupe and watermelon.
As with the
tomatoes, three successive plantings of one-half the
greenhouse
are made. The melons
produce fruit approximately 90 days after
planting the seed.
Harvesting takes place over a two week period.
Each plant produces an average of 10 melons.
At 18 plants per
bed, there is a yield of 48,600 melons a year.
Melon seed is planted in March, directly into the growing
beds,
and the plants grow up trellises.
Melons like temperatures of 75
degrees Fahrenheit (25 Centigrade), so the temperature is
raised
in the greenhouse by a few degrees during that month.
Melons are
harvested over a two-week period.
They have a predicted harvest
date of 90 days, but they are not as highly perishable as
tomatoes.
Melons are sent to market in two shipments, one per week.
The mushroom crop is one of the most profitable crops
produced in
the sample greenhouse.
The ushrooms are not grown hydroponically,
but rather in two layers underneath the growing beds, making
maximum use of space.
They need little or no light.
The space
underneath every bed in the greenhouse is divided into two
shelves with a heavy wire mesh.
Two crops are produced a year.
Two special machines--a choke feeder and a compost
turner--are
used to prepare the growing medium for the mushrooms.
The
machines are not very complicated and could probably be
manufactured
locally in many areas.
The compost used must not contain
any heavy metals since it is used for food production, so
city
wastes cannot be used.
The compost is placed into the choke feeder, which in turn
pushes
it into the compost turner.
The compost turner must be kept moist
and the turning activated every four to five days for two
weeks.
After that, the trays can be filled.
For one week they are left
to "sweat out."
During this time the temperature of the compost
rises and the mushroom spawn can be planted.
Once the spawn has been planted, it is best to maintain a
temperature
of approximately 70 degrees Fahrenheit (20 C) for three
weeks. After that,
the trays should be covered with one inch (2.5
cm) of topsoil, the temperature in the greenhouse lowered a
few
degrees, and the trays watered well.
Mushrooms are harvested on a
daily basis, beginning approximately one month later.
From the
time the trays are filled, there is a two month growing
period.
Harvesting lasts approximately 45 days.
Mushrooms are planted in
August and December.
The compost and soil material left over from the mushroom
production
is used for the production of seedlings.
One whole section
of the greenhouse is devoted to seedlings, which are sold in
the
spring on a retail basis.
They are a profitable product since
seeds are inexpensive and the compost material is
recycled. Seedlings
are grown with roses in two 18-bed clusters.
The seedlings
occupy the area for a three-month period.
During the other nine
months the area is used for research and development of new
crops. The seedlings
receive the same nutrient feeding as the
rest of the greenhouse, although they sit on top of the
gravel in
the beds.
The greenhouse produces seedlings of the most common plants
that
local gardeners tend to buy as plants rather than grow from
seed
themselves. The main
crop comes from the tomato seed saved from
the production of tomatoes.
Six growing beds are used for the
tomato seedlings, two for sweet peppers, one for hot
peppers, two
for broccoli, two cauliflower, two cabbage, one for melons,
one
marigold, and one for various types of squash and flowers.
Long-stem roses are grown in nine beds holding 75 bushes
each.
Seven beds are for red roses, one is for yellow, and one
pink.
This works out to 80 percent red, 10 percent yellow, and 10
percent
pink. Each bush
produces two roses four times a year, for a
total yield of 5,400 roses.
Half the roses are planted in October, and the three-month
production
schedule produces roses at the holidays of Christmas
(December), Easter (March or April), July 4th, and again in
October.
The second planting is made in November, producing flowers
for Valentine's Day (February 14), Mother's Day (May), and
the
end of August. The
blooming can be accurately controlled by pruning
and pinching at the right times.
The rose bushes need to be
replaced every five years.
They need eight hours of light a day
to produce flowers, so in the winter, fluorescent lights are
used
throughout the day.
The greenhouse is experimenting with other flowers as
well. Carnations
root easily, produce heavily, and the flowers last a long
time. They grow
three feet tall and like a lot of light.
The lily
can be a hardy perennial if it is grown from bulbs or
tubers. It
also likes a lot of sunlight and takes at least two years to
produce flowers.
Snapdragons are also being tested, and orchids
are a long-term project, taking from three to seven years to
bloom. Orchid
production is expected to be very profitable, for
both plants and blossoms.
The terrestrial variety loves an airy
growing medium, and does well in inert growing materials.
Local research and development efforts are needed to
determine
the types of crops and products that can be successfully
grown
and marketed, and the composition and sources for the
nutrient
solutions to support them.
IV. MARKETING
Marketing is obviously a very important question for a
hydroponics
enterprise. There
must be local demand for a product, or good
transportation service to get the produce to distant
customers.
Perishable produce must be marketed with a minimum of
delay. Production
of off-season crops is likely to find ready local markets,
when field-grown produce transported from distant places is
expensive.
Hydroponic vegetables are labelled when they are packed for
retail
sales to identify them as hydroponically-grown, vine-ripened
produce. This has
been a major marketing factor in selling the
produce, where hydroponically-grown produce has become known
and
is popular with buyers for its excellent flavor, good color,
and
perfect shape.
The local market potential should be thoroughly examined
before
undertaking a business venture.
Do most of the local businesses
buy their produce from wholesalers? Is there an interest in
high
quality, off-season produce, or special items? Are there
hotels
or specialty restaurants that might be interested in
contracting
for specific crops? Businesses may be interested in
bypassing the
wholesalers for a higher quality product.
The hydroponics greenhouse
may consider selling produce to wholesalers at the
greenhouse,
avoiding transportation costs.
The enterprise may start
out in the wholesale market and move into the retail market
as
the business grows.
There may be seasonal markets which can be served by the
hydroponics
greenhouse enterprise, such as flowers for holidays or
seedlings
in the Spring. In
this case advertising on local radio and
in area newspapers should be considered.
Advertising at the greenhouse should include an
informational
brochure to show the advantages and superior products of
hydroponics.
The brochure can also be placed at information centers and
major tourist areas within 100 miles (60 km) of the greenhouse.
Advertisements on local radio or in local newspapers help to
inform the public about the operation of a hydroponics
greenhouse.
Printed advertisements have the added advantage of showing
the public the name and logo of the company.
If possible, packaging for the produce should bear the
company's
logo. Depending on
what crops are selected, it may be possible to
use one size of box for all the produce that has to be
shipped.
V. ORGANIZATION
A medium- to large-scale hydroponics enterprise needs staff
in
each of the areas described below.
A smaller operation would need
to consider these work areas and assign one or more persons
as
appropriate.
o Manager--responsible for purchasing, public relations,
sales,
and personnel;
o Supervisor--with training in horticulture, responsible for
disease and
parasite control, crop selection and scheduling,
maintaining the
nutrient supply and the growing environment,
and for research
and development;
o Maintenance--responsible for maintenance and repair of the
nutrient system,
growing beds, and environmental systems;
o Secretary--responsible for maintaining records, personnel
files,
correspondence, and acting as receptionist;
o Laborer--maintaining the plants and growing beds,
harvesting,
packing, and
storing the crops.
o Bookkeeping or accounting services may also be needed.
VI. SUPPLIERS AND
MANUFACTURERS
Johnny's Selected Seeds
299 Foss Hill Road
Albion, Maine 04910
Stokes Seeds -- tomatoes
Box 548
Buffalo, New York 14240 USA
Willhite Seed Company -- cantaloupe and melon seeds
P.O. Box 23
Poolville, Texas 76076 USA
Hydroponic and Greenhouse Supplies, Division of E.R.I., Inc.
6433 Sepulveda Blvd.
Van Nuys, California 94101 USA
Hydroponic Industries, Inc.
5650 S. Syracuse Circle
Englewood, Colorado 80110 USA
BIBLIOGRAPHY
Boyle, G. and Harper, P. Radical Technology.
Gloucester, Massachusetts:
Undercurrents
Books, 1976.
Dale, E. Management: Theory and Practice.
New York: McGraw Hill,
1973.
DeKorne, J. Survival
Greenhouse. PeacePress, 1975
Dickerman, Alexandra and John.
Discovering Hydroponic Gardening.
Santa Barbara, CA:
Woodbridge Press Publishing Company, 1975.
Douglas, J.S.
Advanced Guide to Hydroponics.
New York: Drake
Publishers, 1976.
Douglas, J.S.
Gardening Without Soil: A Complete Guide to Hydroponics.
New York: KeyBook
Publishing Co., 1977.
Dutta, R. Water
Gardenina Indoors and Out. New York:
Crown Publishers,
1977.
Ellis, C. and Swaney, M.W. Soilless Growth of Plants.
New York:
Reinhold
Publishing, 1947.
Hanan, J.J., Holley, W.D., and Goldsberry, K.L.
Greenhouse Management.
New York:
Springer-Verlag, 1978.
Laughans, R.W.
Greenhouse Management: A Guide to Structures,
Environmental
Control, Materials Handling, Crop Programming.
and Business
Analysis. Ithaca, New York: Halcyon
Press, 1980.
Marvel, M.E.
Hydroponic Culture of Vegetable Crops. Gainesville,
Florida:
Agricultural Extension Service, University of Florida,
1966.
McCullagh, J.C. The
Solar Greenhouse Book. Emmaus,
Pennsylvania:
Rodale Press, 1978.
Nelson, K.S.
Greenhouse Management for Flower and Plant Production.
Danville, IL.: The
Interstate Printers and Publishers,
1973.
Parsins, R. Small
Plastic Greenhouses. Berkeley:
University of:
California Press,
1975.
Rodale, R., ed.
Organic Gardening Encyclopedia.
Emmaus, Pennsylvania:
Rodale Press, 1980.
Schwarz, M. Guide to
Commercial Hydroponics. Jerusalem:
Israel
University Press,
1968.
Stokes Seed Company Catalogue, Buffalo, New York, 1981.
Turner, W. I. and Henry, V. M.
Growing Plants in Nutrient Solutions.
New York: John
Wiley and Sons, 1939.
United States Department of Agriculture, Agricultural
Research
Service Growing
Crops Without Soil. Beltsville,
Maryland:
USDA, 1970.
Yanda, B. The Food
and Heat Producing Greenhouse. Santa
Fe, New
Mexico: John Muir
Publications, 1977.
========================================
========================================